In Gartner’s “Digital Transformation: How to Scope and Execute Strategy,” the authors make a critical point: all too often, organizations are unable to effectively and efficiently complete their digital transformation journey. A digital transformation platform can solve this problem.
In fact, this research quotes another Gartner asset, “A Digital Business Technology Platform Is Fundamental to Scaling Digital Business,” which confirms this hypothesis.
But what exactly is a digital transformation platform, specifically in the context of manufacturing and industrial organizations? And how can this platform add value to your organization?
We’ll explore these questions, including a real-world case study and actionable insights.
What Is A Digital Transformation Platform?
A digital transformation platform is a centralized system of technologies and tools built to help organizations modernize their processes and workflows. It’s designed to increase efficiency, innovation, and competitiveness.
In a manufacturing and industrial context, these platforms are often needed to digitize legacy processes, enable data-driven decision-making, and ensure collaboration across teams and departments.
For industrial and manufacturing organizations, a digital transformation platform can include:
- Knowledge digitization and management: Centralizing institutional knowledge for easy access and continuous value-add.
- AI-Powered insights: Leveraging AI to extract actionable insights from structured and unstructured data.
- Automation and workflow optimization: Streamlining processes to reduce manual tasks and operational costs.
- Interoperability and scalability: Seamlessly integrating with existing systems and scaling to meet future needs.
- Data privacy and security: Ensuring compliance with industry regulations and safeguarding sensitive information.
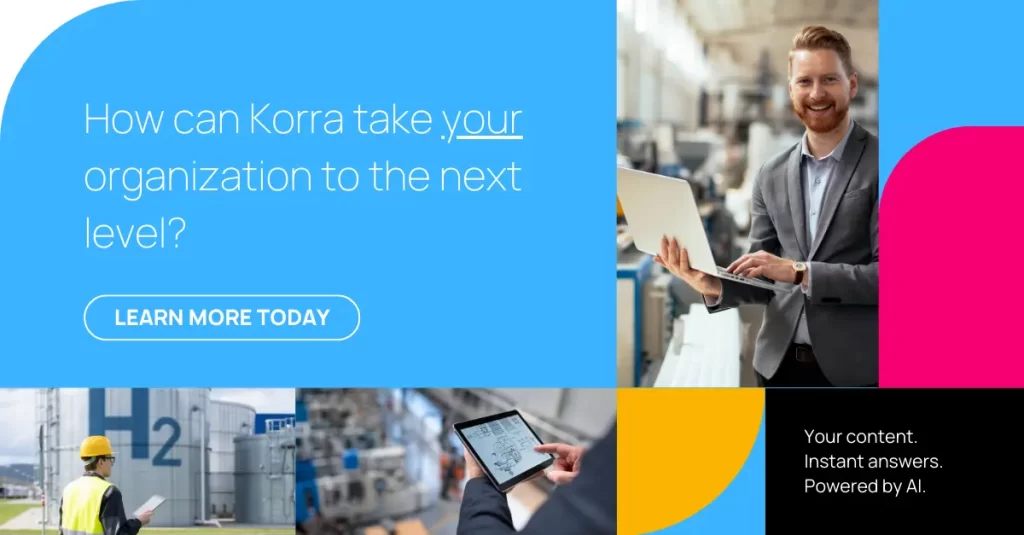
Why Is A Digital Transformation Platform Important?
A digital transformation platform is crucial for manufacturing and industrial organizations because it directly addresses the unique challenges of these sectors: complex workflows, legacy systems, and siloed knowledge. It can unlock opportunities for operational efficiency by drawing from the entirety of organizational knowledge to add tremendous value. Key benefits include:
1. Enhanced Operational Efficiency
By centralizing institutional knowledge and enabling AI-driven search and insights, digital transformation platforms can reduce the time needed to resolve maintenance issues, troubleshoot equipment failures, and address production delays.
2. Break Down Knowledge Silos
Manufacturing environments often have fragmented data across maintenance logs, manuals, legacy systems, and employee expertise. Digital transformation platforms consolidate this knowledge, ensuring employees can quickly find the information they need.
3. Support Scalability and Agility
Modern, scalable digital transformation platforms integrate with legacy systems and modern cloud infrastructure, allowing companies to evolve without overhauling their entire IT landscape.
Additionally, real-time access to data and insights empowers organizational leadership to make faster, more informed decisions, responding quickly to market changes or production challenges.
4. Ensure Compliance and Security
With strict regulatory requirements in many –if not most – industrial and manufacturing environments, digital transformation platforms ensure that processes and documentation meet compliance standards, while advanced security measures protect sensitive information.
Bottom Line: ROI and Competitiveness
Ultimately, digital transformation platforms deliver measurable ROI through increased productivity, reduced operational costs, and faster time-to-market.
As Doug Shannon notes, quoted in CIO.com: the vast majority of enterprises are now focused on two categories of use cases that are most likely to deliver positive ROI. One being knowledge management (KM), consisting of collecting enterprise information, categorizing it, and feeding it to a model that allows users to query it. And the other is retrieval augmented generation (RAG) models, where pieces of data from a larger source are vectorized to allow users to “talk” to the data. For example, they can take a thousand-page document, have it ingested by the model, and then ask the model questions about it.
Introducing Korra as The Digital Transformation Platform for Manufacturers
Korra stands out as a purpose-built digital transformation platform designed to meet the unique needs of manufacturing and industrial organizations. It unlocks institutional knowledge and streamlines information discovery, empowering teams to make faster, smarter decisions – improving operational efficiency, reducing downtime, and enhancing productivity.
Korra is able to digitize and centralize critical knowledge from disparate knowledge sources, including technical manuals, maintenance logs, videos, PDFs, equipment documentation, and internal systems.
Its advanced AI-powered search and insights capabilities ensure that employees can quickly find accurate information, reducing troubleshooting time and minimizing production delays. Unlike traditional knowledge management systems, Korra goes beyond simple search functions by providing contextual information and intuitive chat functionality.
Crucially, Korra aligns with the specific security and compliance needs of industrial environments. Its scalable architecture ensures that as organizations grow, their digital transformation efforts can scale accordingly.
A Digital Transformation Platform in Action
Wedge, part of United Rentals’ Advanced Solutions Group, sought to modernize its knowledge base to better support internal field technicians and external contractors.
Their existing system struggled with limited media capabilities, a cumbersome interface, and the absence of AI-driven assistance and SSO integration. These limitations slowed troubleshooting, increased reliance on direct support, and made it challenging to scale their knowledge management as the organization grew.
To address these challenges, Wedge implemented Korra’s AI-powered knowledge platform, which offered a scalable, user-friendly interface with rich media support, tailored knowledge paths, and secure SSO access.
The results were transformative: Korra resolved 70%-80% of users’ basic troubleshooting needs without email or phone support, reducing repetitive queries by 8%0-90%. Field technicians and managers used Korra to quickly access troubleshooting guides and training materials, while external contractors independently resolved on-site issues, improving productivity and reducing downtime.
Additionally, new hires benefited from faster onboarding with instant access to accurate information. With reliable search results and AI-driven insights, Wedge achieved measurable ROI through lower training costs, reduced support demand, and scalable knowledge management; positioning the company for sustained growth and operational efficiency.
Conclusion: Korra as the First Step in Unlocking Value from Digital Transformation
In essence, Korra transforms how manufacturing teams access, apply, and share knowledge. It breaks down knowledge silos, helping industrial organizations drive measurable ROI from their digital transformation initiatives.Try it for yourself: click here.